On introduces inductive position sensors for the industrial and transportation markets
Time:2024-04-29
Views:147
Source: ON Advanced Solutions (ASG) By Bob Card
With the increasing degree of automation in all walks of life, the importance of motion control is becoming increasingly prominent. In order to drive the motor effectively, control inputs describing speed and position are essential. However, there are a variety of technologies to achieve this sensing, each with different characteristics and application scenarios.
This article will compare the different rotation sensing techniques and discuss the reasons for choosing them. Then, we‘ll look at some of the latest devices on the market.
Position sensing applications
In order to improve accuracy, improve yield, and reduce operating costs, many processes that previously required manual operation have been automated, which has led to a rapid growth in location sensing applications. In fact, as long as there is some form of motion, there needs to be sensors that provide position information to the controller.
Industry 4.0 has driven many advances in automation in the industrial market. Robotics is becoming increasingly common, enabling "unmanned" operation around the clock without fatigue or error - which requires a sensor for each axis of motion. The same goes for "collaborative robots" that work alongside humans in traditional factories.
Today, many parts are made by machine-some using numerical control (CNC) machines, some using laser cutters, and some using 3D printers. These machines have moving parts and require precise position control to meet quality objectives. Once parts are machined, they are often transported via automated material handling or conveyor belts, which also require position sensing.
Position control is also needed in many places outside the factory, such as large medical equipment that can move patients or scanners. In addition, robots are now able to perform surgery, which also requires very precise control.
In the transportation sector, every application involves motion. Whether it is traditional transportation such as trains, agricultural machinery, construction machinery, or emerging applications such as autonomous mobile robots (AMRs) in warehousing and thousands of drones, location sensing is required.
As passenger cars with all modes of drive (internal combustion engine (ICE), pure electric drive (EV) and hybrid) are moving towards electrification, mechanical control solutions are being replaced by systems such as "drive-by-wire" and "steering-by-wire". For these systems to function properly, the position information of the accelerator pedal (accelerator) must be transmitted to the electronic control unit (ECU), or the position information of the steering wheel must be transmitted to the steering control system.
As electronic control extends to almost all aspects of vehicle operation, position sensing technology is also widely used in suspension components (for level/ride control), powertrains, and power Windows, sunroofs, door locks, and more.
Comparison of position sensing techniques
Rotary position sensing mainly uses three technologies - optical, magnetic and inductive technologies, each of which has its own different operating modes, advantages, disadvantages and application scenarios.
Optical encoders, often considered the most accurate (though not in all cases), work by passing light through a disk with holes, using pulses of light to detect motion as the disk rotates.
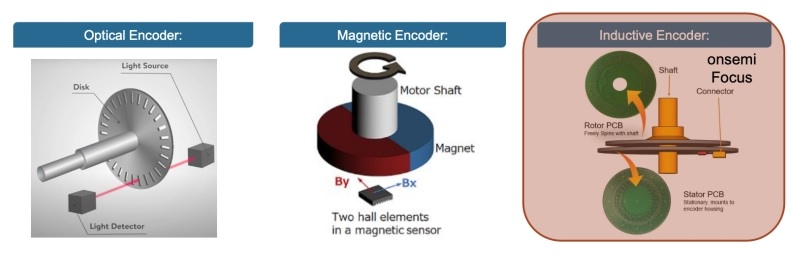
Figure 1: The main methods of rotation position sensing include optical, magnetic and inductive techniques
Typically, such devices are used in applications that require extremely high precision, such as precision robots and machine tools such as CNC lathes or laser cutters. Although they are highly accurate and not sensitive to magnetic fields, they are susceptible to vibrations and dirt on the disc, factors that can cause them to fail.
Magnetic encoders tend to be less accurate and are mainly used in applications that are very cost sensitive. They perform well in the presence of vibration and pollution, but external magnetic fields can cause significant effects on them, which limits their scope of application.
Inductive encoders are more accurate than magnetic encoders, can withstand a higher degree of vibration and pollution, and are not sensitive to magnetic fields. Other advantages include: good repeatability, temperature insensitive, small number of devices, small size, and no need for rare earth materials (i.e. magnets).
NCS32100 dual inductive position sensor
onsemi‘s NCS32100 dual inductive position sensor delivers excellent non-contact position accuracy with two simple and innovative PCB discs, better than +50 arcseconds or 0.0138 degrees of mechanical rotation. One PCB is fixed to the motor stator (the stationary part), while the other single-layer PCB is fixed to the rotor or shaft. The two PCBS are placed in parallel, separated by an air gap of 0.1mm to 2.5mm. The NCS32100 is located on the stator PCB.
Thick and thin (double) conductive wires or coils are printed on two disk surfaces. The third conductive trace, called the excitation coil, is printed on the stator PCB. The NCS32100 sends a 4MHz sine wave to the excitation coil to generate an electromagnetic field around the stator excitation coil. According to Faraday‘s law of mutual inductance, the rotor‘s thick and thin wire winding intersects the electromagnetic field, coupling energy into the rotor coil and forming eddy currents.
At the same time, the stator‘s thick and thin coils are connected to up to eight NCS32100 receiver inputs. When the rotor rotates, the rotor eddy current interferes with the stator receiving coil. The NCS32100 processes these disturbances through a proprietary algorithm of its internal DSP (digital signal processor) to measure the rotor position.
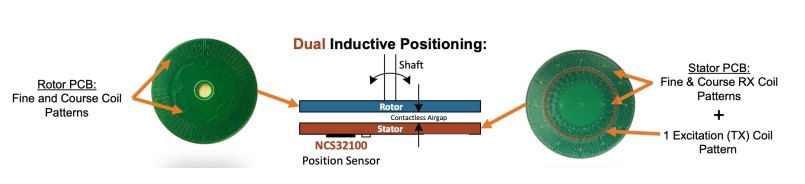
Figure 2: Dual inductance technology provides high performance with a simple solution
Using a 40mm PCB sensor, the NCS32100 achieves a position accuracy of ±50 arcseconds at 6,000 RPM, up to 45,000 RPM at the expense of some accuracy. Using a larger PCB sensor or precisely aligning the rotor with the stator, greater accuracy up to +/- 10 arcseconds can be achieved.
This simple solution uses only a small number of electronics, thus ensuring a small size and low cost. In addition, it is completely insensitive to temperature fluctuations, pollution and external magnetic fields.
Dual inductance technology integration scheme
On‘s NCS32100 supports high-precision rotary position sensors designed for industrial applications and environments. It is an absolute position device that determines its position without movement. The NCS32100 is also capable of calculating speed at speeds up to 45,000 RPM.
At speeds of up to 6,000 RPM, the NCS32100 provides a full accuracy of ±50 arcseconds, comparable to the performance of many optical encoders. The device also integrates Arm? Cortex? M0+ MCU provides highly configurable and internal temperature sensors.
The NCS32100‘s built-in calibration routine allows the sensor to self-calibrate with a single command in just two seconds. It does not need to refer to the encoder, as long as the rotor speed is between 100 and 1000 RPM, the program can run at any time. All calibration coefficients are stored in non-volatile memory (NVM).
Typical optical solutions require a total of three PCBS - optical discs, stator PCBS, and LED driver PCBS - and about 100 devices to achieve full functionality.

Figure 3: Dual inductor technology is comparable in accuracy to optical technology, while being less complex and costly
In contrast, the NC32100-based scheme requires only two PCBS: the rotor is a single-layer PCB with no devices, while the stator PCB contains only 12 devices.
In automotive applications, while cost and reliability are important, safety is even more critical, especially in applications such as steering or braking. On‘s automotive-grade absolute position sensor, the NCV77320, is ISO26262 compliant and has been specifically designed for these critical applications. The NCV77320 has a position accuracy of 194.3 arcseconds or 0.0539 degrees of mechanical rotation (depending on the PCB geometry), mainly because it has only three receiver inputs, compared to eight receiver inputs for the NCS32100. And the NCV77320 does not support thick or thin coil PCB configuration. Both the NCV77320 and NCS32100 can operate as rotary or linear encoders.
Applications for the NCV77320 include brake pedal sensors, accelerator pedal sensors, motor position sensors, brake system sensors, vehicle level sensors, transmission gear sensors, accelerator position sensors, and exhaust gas recirculation valve sensors.
Like the NCS32100, the NCV77320 is not sensitive to pollution, temperature changes, and magnetic field interference, and can be used in automotive environments with ambient temperatures ranging from -40oC to +150oC.
The NCV77320 is capable of operating at speeds up to 10,800 RPM and communicating with companion MCUS via SENT, SPI, or analog interfaces.
Sum up
With the increasing popularity of automation, there is an increasing demand for position sensing of rotary motors. There are several technologies that enable this, including optical, magnetic, and inductive technologies. Optical technology is highly accurate, but expensive and susceptible to contamination. Magnetic technology is low cost, but prone to magnetic field interference.
Inductance technology is increasingly in favor, and with the advent of dual-inductance sensors, it is now possible to create sensors that are both optically accurate and more cost-effective.
Disclaimer: This article is transferred from other platforms and does not represent the views and positions of this site. If there is any infringement or objection, please contact us to delete it. thank you! |