DRV10987: Motor start failed when enabling ISD
Time:2023-09-12
Views:703
When initial speed detection (ISD) is enabled, motor start faults may occur in DRV10975, DRV10983, DRV10987, and DRV10983-Q1. The reason for this issue is that the device has a comparator on the phases (U, V, and W) to check if the motor is still rotating. In essence, when the rotor bypasses the stator, a back electromotive force voltage (BEMF) is generated in phase, and the device comparator checks the number of times the back electromotive force crosses zero to detect whether the rotor is rotating. If ISD is enabled, the device will see the rotor rotating, attempting to resynchronize with the rotor and drive the motor.
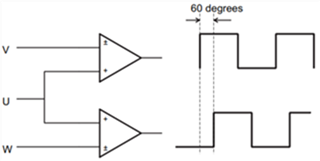
BEMF comparator
When the rotor is not actually rotating, the device will detect a certain rotor speed (displayed in the speed command buffer register). This situation occurs when there is noise in the motor phase, which is coupled to the BEMF comparator. The device attempted to resynchronize but failed due to insufficient BEMF signal, and then attempted to resynchronize again. This can cause the drive to get stuck. Applying external thrust to manually rotate the motor will cause the device to detach from this state and start rotating the motor.
There are two ways to solve this problem:
1. Disable ISD
2. Find a method to reduce noise coupled to the phase
Here are some suggestions for reducing phase coupling noise:
Increase BEMF comparator hysteresis. The 0x92 [12] of the Config3 register in DRV10987 is the BEMF comparator hysteresis option. Setting this bit to "1" will increase hysteresis. When the hysteresis is higher, the comparator is less likely to switch from random noise. We strongly recommend that you perform this action.
If you are using a voltage regulator in buck mode (using an external inductor), please use a shielded inductor. Experiments have shown that the inductor on the circuit board can be used as an antenna to pick up noise from the environment and various phase windings of the motor. Shielding helps prevent external noise pickup.
Remove the inductor and use an external resistor to place the voltage regulator in linear mode. Compared to inductors, resistors pick up much less external noise. If VREG does not power any external components, it is recommended to use this method.
Optimize the layout to have sufficient GND planes to prevent switching noise. Switching circuits based on GND (such as VREG) will generate a large number of ripples on the ground plane. Optimize the layout so that the switching noise on the grounding plane is not coupled with phase, thereby improving performance.
Disclaimer: This article is transferred from other platforms and does not represent the views and positions of this site. If there is any infringement or objection, please contact us to delete it. thank you! |