Why is motor drive a key technology for industrial enterprises to achieve carbon neutrality
Time:2023-11-20
Views:592
Author: Doctor M
Not long ago, the World Meteorological Organization (WMO) stated in its latest meteorological report that there is a 50% probability that the global average annual temperature will be temporarily 1.5 degrees Celsius higher than pre industrial levels for at least one year in the next five years. The organization suggests that this will have serious impacts, with 70% -90% of coral reefs disappearing, sea level rise, and so on. The increase in carbon dioxide content is the biggest culprit.
In order to avoid a further increase in global average annual temperature, break through the 2 degree Celsius target set by the Paris Agreement, and achieve "carbon neutrality" in the second half of the 21st century, it is not only the international responsibility of countries around the world, but also a must to reduce the threat to human survival.
To achieve the goal of "carbon neutrality", every high energy consuming link needs to be improved, such as electric motors. According to a recent survey by the International Energy Agency, electric motors account for approximately two-thirds of industrial electricity consumption and approximately 46% of global electricity consumption. Therefore, improving motor energy efficiency and efficiently driving motors is the key to achieving "carbon neutrality". Today we will talk about how to systematically improve motor energy efficiency, and how the electronic components available on the Trade Electronics website can help designers.
Efficient motors assist in "carbon neutrality"
Electric motor refers to an electromagnetic device that converts or transmits electrical energy based on the law of electromagnetic induction. From the definition, it can be seen that motors are driven by electricity, and as reflected in the above data, motors are the single largest type of device in the world in terms of electricity consumption.
The above data has already mentioned that motor power consumption accounts for a high proportion of global industrial power consumption, and the situation is similar in China. Statistical data shows that China‘s electric motors consume 69% of the total electricity consumption in society and 75% of industrial electricity annually. The main reason for this situation is the insufficient penetration rate of green motors in China. According to the "Motor Energy Efficiency Improvement Plan 2018", the penetration rate of high-efficiency motors in China in 2018 was only 3%. Referring to data from the China Federation of Industrial Economics, this key indicator is still less than 10%. The 2022 Industrial Energy Efficiency Improvement Plan requires that the proportion of newly added high-efficiency motors should reach over 70% by 2025.
If high-efficiency motors can be popularized, it will be of great significance for achieving the goal of "carbon neutrality". According to data from the National Bureau of Statistics of China, thermal power generation accounted for 71.13% of the total power generation in 2021. Globally, in 2021, fossil energy power generation accounted for 62% of the total electricity generation worldwide. From this perspective, motors indirectly lead to an increase in global carbon dioxide content. Improving motor energy efficiency will significantly reduce energy demand and reduce global carbon dioxide emissions.
If you want to improve the energy efficiency level of the motor, you can first consider from the perspective of motor adaptation. For example, permanent magnet synchronous motors are more suitable for application scenarios with frequent load changes and frequent no-load situations, such as lathes, machine tools, and wire drawing equipment, which can achieve good energy-saving effects.
From the perspective of motor design, it is also possible to reduce losses and improve heat dissipation by improving relevant designs. The losses of general motors mainly include the following types - iron core losses, stator/rotor copper losses, wind wear losses, and stray losses, and each link has room for continuous improvement. For example, motors using copper windings can significantly reduce the winding of copper wires by increasing their diameter, thereby reducing losses and reducing heat dissipation.
In order to reduce the energy consumption of motors, manufacturers will also develop energy-saving technologies, and variable frequency speed regulation is a typical energy-saving technology. During the operation of traditional motors, when the load is significantly reduced or unloaded, the input power does not change, but the output power changes, which wastes a large amount of electrical energy. By adopting frequency conversion technology, the energy efficiency of the motor can be significantly improved. According to data from relevant motor manufacturers, frequency conversion technology can generally save 10% -50% of electricity.
In addition, a more intelligent and precise motor control system can also help improve motor energy efficiency. Motor control emphasizes "one rise and one drop", where "one rise" refers to improving the efficiency of motor FOC (field oriented control) control algorithms, and "one drop" refers to reducing power device losses and motor losses. At present, a combination of deep learning and artificial intelligence algorithms has been widely used in motor FOC control algorithms, which can continuously optimize the efficiency of the motor, improve the accuracy of control positions, and reduce unnecessary current losses.
Finally, let‘s talk about our "protagonist" today - electric motor drive. After observing the solutions of major original factories, it is not difficult to find that "motor control and drive" are currently a fusion concept, which is actually easy to understand because motor control is a "decision-making system" and strongly related to control algorithms, while motor drive is an "execution system". The latter receives the control signal of the former, then rotates the motor to a specific angle and sends it to a specific position. The motor drive has a dedicated driver and supporting drive circuit. To improve the energy efficiency of the motor from this point, we need to start from the following aspects.
For motor drivers, drivers with low conduction and switching losses can help designers significantly reduce system losses, and the frequency conversion of motor drives is also a major trend. For example, in the drive of AC motors, electronic speed control and higher drive energy efficiency can also be achieved by replacing single speed control with variable frequency drives. In terms of supporting circuits, specially optimized circuit structures can often achieve good energy-saving effects. For example, in the use of bridge circuits in motor drive circuits, we further take automobile motor drive as an example. Here, the drive system is actually an inverter, and multiple half bridge circuits are often used in the inverter circuit to improve system efficiency. Another important direction is to increase the input voltage value of the motor, which can greatly reduce the loss of the motor during the constant power period. However, this trend also puts higher requirements on the motor drive protection circuit, requiring higher performance protection components.
By using the above methods, the energy consumption of the motor can be significantly reduced, which has enormous empowering value for achieving the goal of "carbon neutrality". Next, let‘s take a look at how the components sold on the Mao Ze Electronic website can play an important role in some specific aspects.
Litteluse gate driver
During the process of motor drive, the driving signal comes from a microcontroller or microprocessor, but this signal cannot directly start the motor drive system and needs to be amplified by a gate driver to amplify the voltage or current. Therefore, gate drivers are the fundamental and indispensable components in motor drive systems.
The first device we recommend today is a gate driver from the manufacturer Litteluse, with the manufacturer number LF2136BTR on the Trade Electronics website.
LF2136BTR
LF2136BTR is a three-phase gate driver IC designed specifically for high-voltage and high-speed applications, which can be used to drive half bridge configurations. This device is built based on high-voltage technology, and the high-voltage side can switch to a high voltage of 600V during bootstrap operation. At the same time, the LF2136BTR has excellent driving, compatibility, and protection characteristics. This device has a high pulse current buffer designed to achieve minimal driver cross conduction; Compatible with CMOS levels (as low as 3.3V), easy to connect to control devices, and enable low levels for better operation in high noise environments; Provide multiple protection functions, including direct protection, undervoltage locking, overcurrent protection, etc.
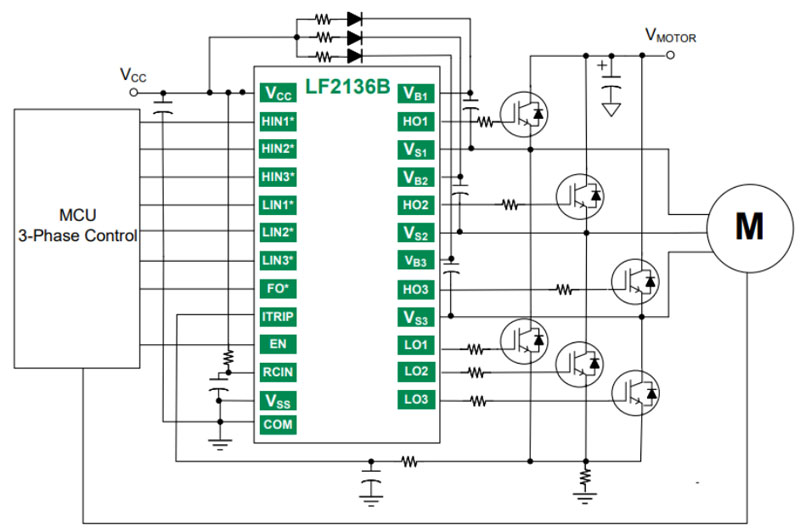
Figure 1: Typical Application Block Diagram of LF2136BTR (Source: Litteluse)
LF2136BTR is a part of the Litteluse gate driver series. In addition to the three-phase gate driver IC, LF2136BTR also includes high-voltage high-speed gate drivers, all of which have high voltage properties, as well as high-quality driving, compatibility, and protection characteristics. They can operate in a wide temperature range of -40 ° C to+125 ° C and can be used to create half bridge gate drivers, three-phase half bridge gate drivers, and high/low side gate drivers. Among them, half bridge gate drivers and high/low side gate drivers can be further designed for applications such as DC-DC converters, AC DC inverter motor control, motor drivers, Class D power amplifiers, etc; The three-phase half bridge gate drive can be used for three-phase motor frequency converter drives, white goods air conditioning, washing machines, refrigerators, industrial motor inverters electric tools, robots, and general three-phase frequency converters.
The high-voltage characteristics of LF2136BTR and the minimum driver cross conduction can play an important role in helping to achieve "carbon neutrality".
Dual H-bridge motor driver
In classic motor drive circuits, one type of circuit has a shape resembling the letter H, as shown in the following figure, and is therefore also known as the "H-bridge drive". Overall, the H-bridge motor drive circuit has outstanding advantages such as high efficiency, directional control, and braking.
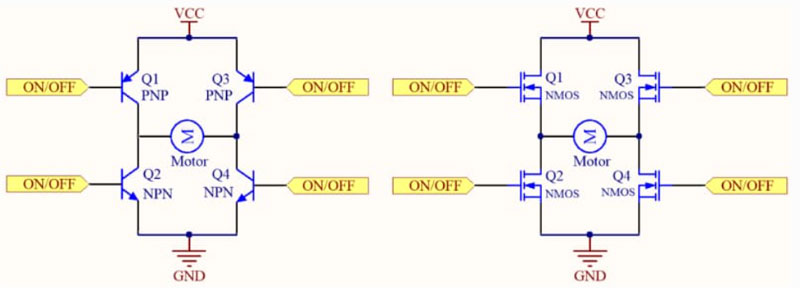
Figure 2: H-Bridge Motor Drive Circuit (Source: Hardware Siege Lion Bowen)
The second device to be introduced today is a dual H-bridge motor driver, from the manufacturer Texas Instruments. The manufacturer number on the Trade Electronics website is DRV8428PPWPR, and you can find this device by searching for this number.
DRV8428PPWPR
DRV8428PPWPR is a dual H-bridge motor driver suitable for various industrial applications, which can be used to drive one bipolar stepper motor, two bidirectional brush DC motors, or four unidirectional brush DC motors. According to different PCB design schemes, this device can drive up to 1A full scale or 0.7A RMS output current.
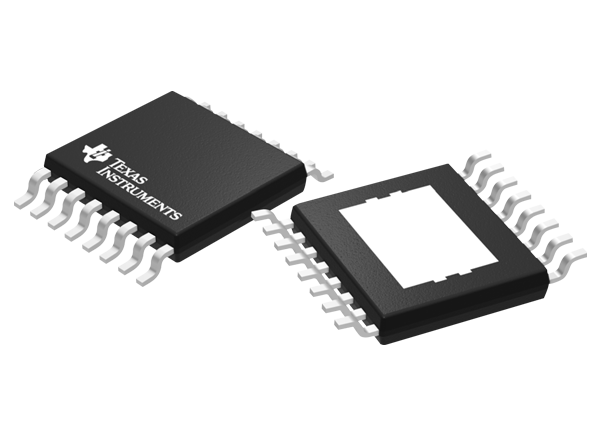
Figure 3: Simplified schematic diagram of DRV8428PPWPR (source: Texas Instruments)
DRV8428PPWPR is a highly integrated device, with an output stage consisting of N-channel power MOSFETs (configured with two full H-bridges), current detection/regulation, and protection circuits. Among them, the integrated current sensing function adopts an internal current mirror architecture, without the need for current detection resistors, and the full range current accuracy is ± 6%; The protection features include VM undervoltage locking, overcurrent protection, and thermal shutdown. In brushed DC applications, surge current limitation can also be achieved. High integration and leading technology enable the DRV8428PPWPR to have a smaller packaging size, smaller board area, and lower system costs.
In terms of application, DRV8428PPWPR‘s leading product features can empower fields such as brush DC motors, printers and scanners, cash registers and EPOS, office and home automation, factory automation and robotics, small appliances, sweeping robots, and humanoid robots.
The DRV8428PPWPR also has many excellent performance to help reduce system power consumption and losses, among which the high integration feature can reduce circuit board and other device consumption. At the same time, the device has a low-power sleep mode, which can achieve ultra-low static current consumption by turning off most of the internal circuits.
Ready to use motor control kit
Next, we will further extend to the introduction of the system solution. Developers have a clear feeling that if there is an excellent development kit available during the solution development process, the entire development process will be greatly accelerated and the product launch cycle will be shortened. And what we will introduce next is a ready-to-use motor control kit.
This kit comes from the manufacturer Infineon Technologies, with the manufacturer number MOTOR-CONTROLKIT12VTOBO1 on the Trade Electronics website.
MOTOR-CONTROLKIT12VTOBO1
Why is MOTOR-CONTROLKIT12VTOBO1 a ready to use kit? Because in the kit, besides MOTIX ™ Embedded power ICs, as well as 360 ° angle sensors and integrated Hall effect switches, are designed for low-voltage motor control applications and can be directly used for rapid prototype design and evaluation.
MOTOR-CONTROLKIT12VTOBO1 can be considered as a TLE9879 evaluation kit, and the TLE9879QXA40 device on top is MOTIX ™ Part of the embedded power IC and single chip three-phase motor driver, system on chip (SoC) solution. This device has a very high level of integration, with internal integration of LIN transceivers, bridge drivers, and power supplies, based on Arm ® The Cortex M3 core is built to support the implementation of advanced motor control algorithms, such as Sensorless Field Oriented Control (FOC).
The angle sensor model on MOTOR-CONTROLKIT12VTOBO1 is TLE 5012B-E1000, which can achieve 360 ° angle measurement with a resolution of 0.01 °. The maximum angle error over the entire service life and temperature range is 1.0 °. The specific model of the integrated Hall effect switch is TLE 4968-1L, specifically designed for high-precision applications. It has excellent power supply voltage capability, using a non regulated power supply, with an overvoltage capacity of up to 42V, without the need for external resistors, and further improves device accuracy through active error compensation. This kit can be used for applications such as pumps, fans, and three-phase BLDC motors.
As mentioned above, MOTOR-CONTROLKIT12VTOBO1 demonstrates its high-precision characteristics in all aspects, which can significantly reduce unnecessary current losses in the system and thereby improve motor energy efficiency.
TVS diode for safer motor control
In order to achieve precise control of the motor and reduce unnecessary energy consumption, the components in the motor control and driving circuit have become increasingly refined, thus requiring more comprehensive protection. Below is a commonly used protective component - TVS diode.
This TVS diode is still from the manufacturer Litteluse, with the manufacturer number SZ1SMA30CAT3G listed on the Trade Electronics website.
SZ1SMA30CAT3G
SZ1SMA30CAT3G is a unidirectional and bidirectional device designed to protect voltage sensitive electronic products from high voltage and high energy transients. This device has excellent clamping ability, high surge capacity, low Zener impedance, and fast response time, with a peak power of up to 400W (1ms) and a maximum forward surge current of 40A.
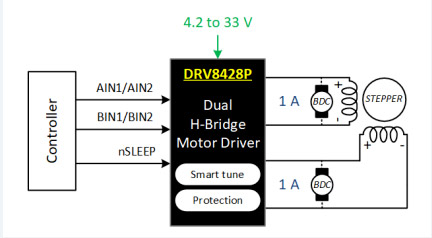
Figure 4: Functional Block Diagram of SZ1SMA30CAT3G (Image Source: Litteluse)
The SZ1SMA30CAT3G adopts Litteluse‘s unique, cost-effective, and highly reliable packaging. Through flat surface treatment, it helps users achieve accurate mounting and can be used in packaging designs for top sliding or bottom circuit board installation.
Through excellent product performance, SZ1SMA30CAT3G can provide more reliable safety protection for motor drives, helping to create more precise control and lower energy consumption motor solutions.
Future Trends in Electric Motor Drive
Achieving the goal of "carbon neutrality" is a long-term and arduous task. As mentioned in the above data, as the largest single energy consuming device, electric motors will continue to grow rapidly in the future with trends such as automotive electrification and industrial automation, and their energy consumption is a key direction that needs to be continuously optimized. Policies of various countries are very concerned about this. For example, in China, in addition to the "Industrial Energy Efficiency Improvement Plan" issued by the Ministry of Industry and Information Technology of China mentioned above, there is also the "Motor Energy Efficiency Improvement Plan" jointly issued by the State Administration for Market Regulation and the Ministry of Industry and Information Technology, which all provide key instructions for improving electrical energy efficiency.
For example, the "Motor Energy Efficiency Improvement Plan (2021-2023)" requires that the production and manufacturing of motor systems, technological innovation, promotion and application, and industrial services be the key directions, actively implement energy-saving transformation and upgrading and energy system optimization, continuously improve the energy efficiency of motor systems, support energy conservation and efficiency improvement in key industries and fields, and help achieve the goals of "carbon peak" and "carbon neutrality".
Facing the future, electric motors will continue to develop towards digitization, lightweight, miniaturization, high efficiency, and high power density, among which motor control and driving play an important role. Therefore, in addition to a significant increase in the shipment volume of motor drive chips and other supporting chips, the technological development trend is also relatively clear. In order to make the external appearance of the entire motor control and drive system more concise and reduce consumables, the integration of related components will be further improved. The motor drive will also be more intelligent and flexible, and the control of each driving wheel of the motor will be independent and accurate; The feedback circuit will be more complete and diverse, making the power output more reasonable; In order to reduce system heating, we will continuously pursue higher pressure driving technology; There is a higher requirement for safety and a high degree of reliability.
Of course, the goal of all these trends is to create more efficient and energy-saving motor systems, and the electronic components sold on the Maoze Electronics website will provide strong support for this, working together with designers to contribute to creating a "green earth".
Disclaimer: This article is transferred from other platforms and does not represent the views and positions of this site. If there is any infringement or objection, please contact us to delete it. thank you! |