What are the advantages of SiC MOSFET for motor drive
Time:2023-12-23
Views:441
Author: Zhao Jia
The following is an example study to verify the advantages of SiC MOSFET in motor drive.
It can be seen that based on the above operating conditions, under the same temperature conditions, the output current of a 30mohm device is 10A higher than that of a 40A IGBT. Even if switched to a smaller 60ohm SiC MOSFET, the output current can be increased by about 5A. Under the same current conditions, the temperature of SiC MOSFT significantly decreases.
In our traditional impression, motor drive systems often use IGBTs as switching devices, while SiC MOSFETs as high-speed devices are often associated with applications that require high-frequency conversion such as photovoltaics and electric vehicle charging. But in specific motor applications, SiC still has incomparable advantages, they are:
1. Low inductance motor
Low inductance motors have many different applications, including atmospheric gap motors, slotless motors, and low leakage induction motors. They can also be used in new motor types that use PCB stators instead of winding stators. These motors require a high switching frequency (50-100kHz) to maintain the required ripple current. However, using insulated gate bipolar transistors (IGBTs) for modulation frequencies above 50kHz cannot meet these requirements. If it is a 380V system, the silicon MOSFET voltage resistance is not sufficient, which opens up new opportunities for wide bandgap devices.
2. High speed motor
Due to their high fundamental frequency, these motors also require high switching frequencies. They are suitable for applications such as high-power density electric vehicles, high pole motors, high-speed motors with high torque density, and megawatt level high-speed motors. Similarly, the maximum switching frequency that IGBT can achieve is limited, and the use of wide bandgap switching devices may be able to overcome these limitations. For example, air compressors in fuel cells. The maximum speed of the air compressor exceeds 150000 rpm, and the output frequency of the air compressor motor controller exceeds 2500Hz. The power device requires a high switching frequency (over 50kHz), so SiC MOSFET is the preferred device for such applications.
3. Severe working conditions
The use of wide bandgap devices in motor controlled inverters has two noteworthy benefits. Firstly, they generate less heat than silicon devices, reducing heat dissipation requirements. Secondly, they can withstand higher operating temperatures - SiC: 600 ° C, GaN: 300 ° C, while silicon chips can only withstand a maximum operating temperature of 200 ° C. Although SiC products currently have some packaging related issues that prevent them from operating at temperatures exceeding 200 ° C, research focused on addressing these issues is currently underway. Therefore, wide bandgap devices are more suitable for motor applications that may face harsh working conditions, such as integrated motor drivers in hybrid electric vehicles (HEVs), underwater and underground applications, space applications, etc
In traditional motor drives, IGBT is often used as a switching device. So, what are the advantages of SiC MOSFET compared to Si IGBT, making it more suitable for motor drive applications?
Firstly, from the perspective of switching characteristics, power device switching losses can be divided into turn-on losses and turn-off losses.
Turn off loss
IGBT is a bipolar device, in which electrons and holes participate in conduction during conduction. However, during turn off, the holes can only gradually disappear through recombination, resulting in a trailing current. The trailing current is the main reason for the large turn off loss of IGBT. SiC MOSFET is a unipolar device, with only electrons participating in conductivity. There is no trailing current during shutdown, resulting in significantly lower shutdown losses for SiC MOSFET compared to IGBT.
Turn-on loss
The instantaneous current when IGBT is turned on often experiences overshoot, which is the reverse recovery current generated during reverse parallel diode commutation. The reverse recovery current superimposed on the turn-on current of the IGBT increases the turn-on loss of the device. The anti parallel diode of IGBT is often Si PiN diode, and the reverse recovery current is more obvious. The structure of SiC MOSFET naturally integrates a diode, without the need for additional parallel diodes. The SiC body diode participates in commutation, and its reverse recovery current is much lower than that of the silicon PiN diode in reverse parallel with IGBT. Therefore, even under the same dv/dt conditions, the turn-on loss of SiC MOSFET is lower than that of IGBT. In addition, SiC MOSFET can integrate servo drivers with motors, eliminating the limitation of dv/dt on cables. Under high dV/dt conditions, the switching loss of SiC will be further reduced, much lower than that of IGBT. Even when the switching process is slow, the switching loss of silicon carbide is better than that of IGBT.
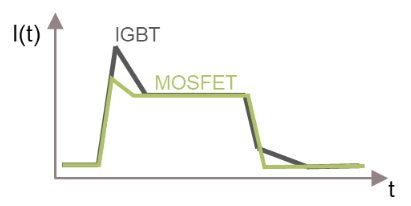
In addition, the switching losses of SiC MOSFETs are basically not affected by temperature, while the switching losses of IGBTs increase significantly with increasing temperature. Therefore, SiC MOSFETs have more advantages in loss at high temperatures.
Considering the limitations of dv/dt, under the same dv/dt conditions, the total switching loss of SiC MOSFET will be reduced by 50% to 60% at high temperatures. If dv/dt is not limited, the total switching loss of SiC can be reduced by up to 90%.
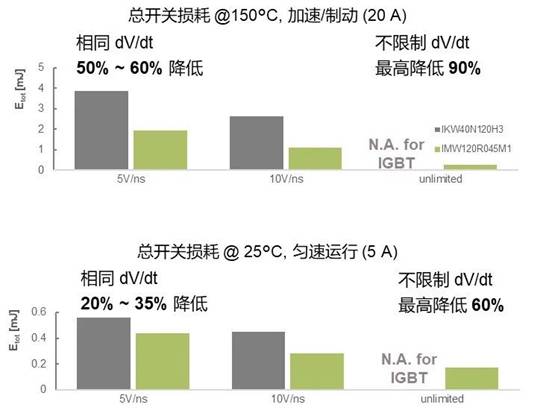
From the perspective of conduction characteristics:
There is no turning point when SiC MOSFET conducts, and a very small VDS voltage can make SiC MOSFET conduct. Therefore, under low current conditions, the conduction voltage of SiC MOSFET is much lower than that of IGBT. When the current is high, the conduction loss of IGBT is lower. This is because as the voltage drop of the device increases, the bipolar device IGBT begins to conduct. Due to the conductivity modulation effect, electron injection excites more holes, and the current rapidly increases, resulting in a steeper slope of the output characteristics. Under light load conditions, SiC MOSFETs have lower conduction losses corresponding to motor operating conditions. Under overload or acceleration conditions, the advantage of SiC MOSFET conduction loss will be reduced.
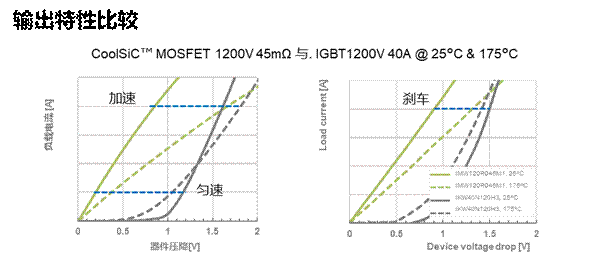
CoolSiC ™ MOSFET reduces conduction loss under various operating conditions,
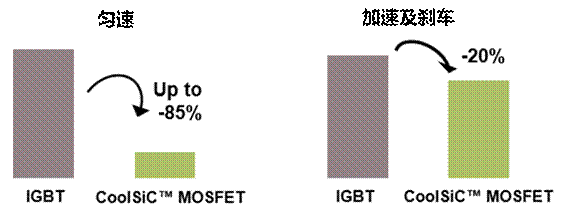
Assuming the following operating conditions, compare the three devices:
IGBT IKW40N120H3,
SiC MOSFET IMW120R060M1H and IMW120R030M1H.
Test conditions
Vdc=600V, VN, out=400V, IN, out=5A-25A,
FN, sin out=50Hz, fsw=4-16kHz, Tamb=25 ° C,
Cos( φ) N=0.9, Rth, HA=0.63K/W, dv/dt=5V/ns
M=1, Vdc=600V, fsin=50Hz, rg@dv /Dt=5V/ns, fsw=8kHz, cable length 5m, Tamb=25 ° C
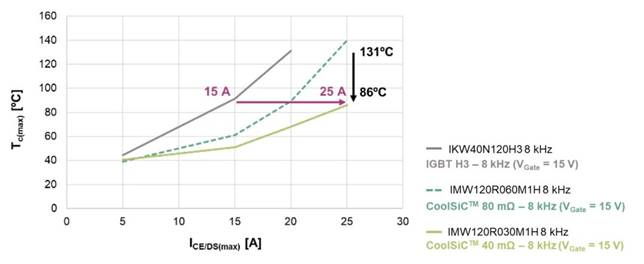
In summary, the benefits that SiC switching devices can bring to motor drive systems are summarized as follows:
·Lower loss - reduces power consumption, making people‘s lives more environmentally friendly and sustainable.
·Excellent performance - achieving higher power density, achieving the same performance with smaller devices to achieve more economical motor design.
·Compact Structure - Achieves a more compact and space saving motor design, reduces material consumption, and reduces heat dissipation requirements.
·Higher quality - SiC inverters have a longer lifespan and are less prone to malfunctions, allowing manufacturers to provide longer warranty periods.
Finally, Infineon CoolSiC ™ It can ensure the short-circuit capability of 3us for a single tube and 2us for an Easy module, further ensuring the safety and reliability of the system.
Disclaimer: This article is transferred from other platforms and does not represent the views and positions of this site. If there is any infringement or objection, please contact us to delete it. thank you! |