Key points and requirements of BMS PCB design for electric vehicles
Time:2024-01-21
Views:359
With the popularization of electric vehicles, Battery Management System (BMS) plays a crucial role in the performance, safety, and lifespan of electric vehicles. BMS is responsible for monitoring the status of batteries, controlling the charging and discharging process, managing battery temperature, and preventing overcharging and discharging to ensure optimal battery performance, safety, and reliability. The BMS PCB design plays a crucial role in ensuring battery performance, safety, and reliability. This article briefly explains the main points and relevant domestic standards and requirements of BMS PCB design for electric vehicles, in order to help PCB engineers better meet the needs of battery management.
GB/T 31485-2015 "General Specification for Battery Management Systems for Electric Vehicles": This standard specifies the performance, reliability, safety, and communication requirements of electric vehicle BMS. These specifications must be followed in the design to ensure the compliance of the BMS.
Key points of BMS PCB design for electric vehicles:
Hierarchical design: Electric vehicle BMS typically includes multiple modules, such as battery management, communication, power management, etc. Therefore, PCB design should adopt a hierarchical structure so that the signals and power lines of different modules can be clearly and effectively separated.
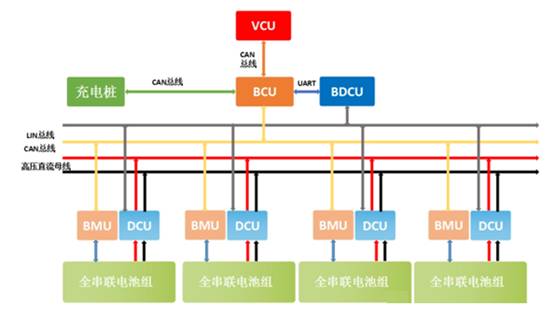
EMC (Electromagnetic Compatibility) considerations: The design of BMS PCB for electric vehicles must consider electromagnetic compatibility to prevent electromagnetic interference from interfering with other vehicle electronic devices and ensure system reliability. In design, shielding measures, ground wire planning, and noise reduction techniques should be taken to reduce electromagnetic radiation and anti-interference ability.
High temperature adaptability: The electric vehicle battery pack operates in high temperature environments, so the BMS PCB must have high temperature resistance performance. The selection of high-temperature resistant materials, reasonable heat dissipation design, and temperature sensors to monitor battery temperature are key.
Safety requirements: BMS is responsible for battery safety management and must meet strict safety requirements. PCB design should consider battery overcharging, over discharging, and short circuit protection to ensure battery safety.
Communication interface: The electric vehicle BMS typically requires data interaction with the vehicle control system, charging station, and monitoring system. Therefore, communication interfaces such as CAN, LIN, and Ethernet should be considered in the design to meet different communication needs.
Maintainability: Electric vehicle BMS requires regular maintenance and upgrades. PCB design should consider features that are easy to maintain, such as clear labeling, easy replacement of components, and modular design.
Low power design: To extend battery life, the BMS should adopt a low-power design. PCB design should pay attention to reducing power consumption, including optimizing circuits, selecting low-power components, and designing sleep modes.
Fault tolerance: The electric vehicle BMS must have a certain level of fault tolerance to prevent the impact of a single point of failure on the entire system. The use of redundant design and fault detection techniques is a common practice.
Domestic BMS specifications and requirements for electric vehicles:
In China, the BMS PCB design of electric vehicles must comply with a series of national and local standards to ensure the safety and performance of electric vehicles. Here are some key specifications and requirements:
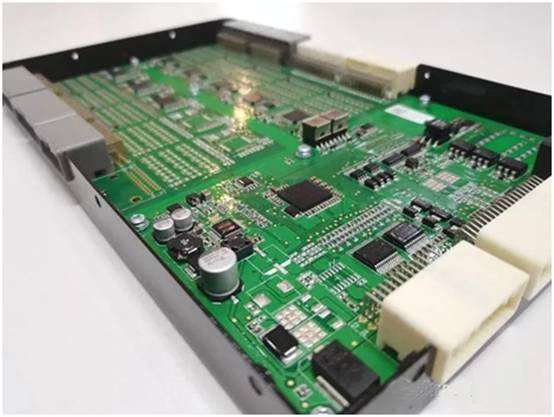
GB/T 31486-2015 "Safety Specification for Lithium ion Power Batteries for Electric Vehicles": This standard specifies the safety requirements for lithium-ion batteries, and the BMS must be able to monitor and manage the battery‘s status to ensure safety.
GB/T 32960-2016 "Technical Requirements for Remote Diagnosis and Communication of Road Vehicles": This standard specifies the requirements for remote diagnosis and communication of electric vehicles, including data transmission of BMS and cloud monitoring. The application of these communication technologies should be considered in the design.
Local standards: Some local governments may establish additional BMS requirements to meet local safety and environmental standards. The design team should closely monitor local regulations and requirements.
Conclusion:
The design of BMS PCB for electric vehicles is a key factor in ensuring battery performance, safety, and reliability. Designers must consider key points such as hierarchical design, EMC, adaptability to high-temperature environments, safety requirements, communication interfaces, maintainability, low-power design, and fault tolerance. At the same time, it is necessary to comply with relevant domestic regulations and requirements, such as GB/T 31485-2015, GB/T 31486-2015, and GB/T 32960-2016, to ensure the compliance of BMS. The future development of electric vehicles requires continuous improvement and innovation in BMS PCB design to meet the growing demand and challenges.
Disclaimer: This article is transferred from other platforms and does not represent the views and positions of this site. If there is any infringement or objection, please contact us to delete it. thank you! |