PCB design skills of dry goods EMC
Time:2022-07-31
Views:1925
Electromagnetic compatibility (EMC) and associated electromagnetic interference (EMI) have always required system design engineers to sharpen their eyes. Nowadays, with the continuous reduction of circuit board design and component packaging, and OEM requirements for higher speed systems, these two major problems are particularly a headache for PCB layout and design engineers.
EMC is closely related to the generation, transmission and reception of electromagnetic energy. EMC is not expected in PCB design. Electromagnetic energy comes from multiple sources, and they are mixed together. Therefore, special care must be taken to ensure that when different circuits, wiring, vias and PCB materials work together, various signals are compatible and will not interfere with each other.
On the other hand, EMI is a destructive effect caused by EMC or unwanted electromagnetic energy. In this electromagnetic environment, PCB designers must ensure to reduce the generation of electromagnetic energy and minimize interference.
Seven skills to avoid electromagnetic problems in PCB design——
Skill 1: PCB grounding
An important way to reduce EMI is to design PCB ground plane. The first step is to make the grounding area within the total area of PCB as large as possible, so as to reduce emission, crosstalk and noise. Special care must be taken when connecting each component to the ground point or ground plane. If this is not done, the neutralization effect of the reliable ground plane cannot be fully utilized.
A particularly complex PCB design has several stable voltages. Ideally, each reference voltage has its own ground plane. However, if there are too many grounding layers, the manufacturing cost of PCB will be increased and the price will be too high. The compromise is to use grounding layers at three to five different locations, and each grounding layer can contain multiple grounding parts. This not only controls the manufacturing cost of circuit boards, but also reduces EMI and EMC.
Low impedance grounding system is very important if you want to minimize EMC. In Multilayer PCB, it is better to have a reliable ground plane rather than a copper thieving or scattered ground plane, because it has low impedance, can provide current path, and is the best reverse signal source.
The length of time the signal returns to the ground is also very important. The time for the signal to and from the signal source must be equal, otherwise the phenomenon similar to the antenna will occur, and the radiated energy will become a part of EMI. Similarly, the route of transmitting current to / from the signal source should be as short as possible. If the length of the source path and the return path are not equal, grounding rebound will occur, which will also produce EMI.
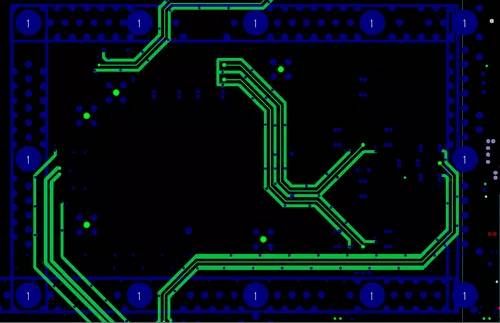
If the time of the signal entering and leaving the signal source is not synchronized, it will produce a phenomenon similar to the antenna, thus radiating energy and causing EMI
Tip 2: differentiate EMI
Due to different EMI, a good EMC design rule is to separate analog circuits from digital circuits. Analog circuits with high amperage or large current should be far away from high-speed wiring or switching signals. If possible, they should be protected with grounding signals. On multi-layer PCB, the wiring of analog wiring should be on one ground plane, while the switch wiring or high-speed wiring should be on another ground plane. Therefore, signals with different characteristics are separated.
Sometimes a low-pass filter can be used to eliminate the high-frequency noise coupled with the surrounding wiring. The filter can suppress noise and return stable current. It is important to separate the ground plane of analog and digital signals. Because analog circuits and digital circuits have their own unique characteristics, it is very important to separate them. Digital signals should have digital grounding, and analog signals should terminate at analog grounding.
In digital circuit design, experienced PCB layout and design engineers will pay special attention to high-speed signals and clocks. At high speed, the signal and clock should be as short as possible and adjacent to the ground plane, because the ground plane can keep crosstalk, noise and radiation in a controllable range, as mentioned earlier.
Digital signals should also be away from the power plane. If the distance is very close, noise or induction will be generated, which will weaken the signal.
Technique 3: crosstalk routing is the key
Wiring is particularly important to ensure the normal flow of current. If the current comes from an oscillator or other similar equipment, it is particularly important to separate the current from the ground plane or not to allow the current to run in parallel with another line. Two parallel high-speed signals will produce EMC and EMI, especially crosstalk. The resistance path must be minimized and the return current path must be as short as possible. The length of the return path route should be the same as that of the transmission route.
For EMI, one is called "violation routing", and the other is "victim routing". Inductive and capacitive coupling will affect the "victim" wiring due to the existence of electromagnetic fields, resulting in forward and reverse currents on the "victim wiring". In this way, ripple will be generated in a stable environment where the transmission length and reception length of the signal are almost the same.
In a well-balanced and stable environment, the induced currents should offset each other to eliminate crosstalk. However, we live in an imperfect world, such a thing will not happen. Therefore, our goal is to keep the crosstalk of all routes to a minimum. If the width between parallel routes is twice the route width, the influence of crosstalk can be minimized. For example, if the route width is 5 mils, the minimum distance between two parallel routes should be 10 mils or more.
With the continuous emergence of new materials and new components, PCB designers must continue to deal with electromagnetic compatibility and interference.
Skill 4: decoupling capacitance
Decoupling capacitors can reduce the adverse effects of crosstalk. They should be located between the power pin and ground pin of the equipment, so as to ensure low AC impedance and reduce noise and crosstalk. In order to achieve low impedance over a wide frequency range, multiple decoupling capacitors should be used.
An important principle for placing decoupling capacitors is that the capacitor with the smallest capacitance value should be as close to the equipment as possible to reduce the inductive impact on the wiring. This particular capacitor is as close to the power pin or power wiring of the equipment as possible, and the bonding pad of the capacitor is directly connected to the via or ground plane. If the wiring is long, please use multiple vias to minimize the grounding impedance.
Tip 5: avoid 90 ° angles
To reduce EMI, avoid 90 ° angle formed by wiring, vias and other components, because the right angle will produce radiation. At this corner, the capacitance will increase, and the characteristic impedance will also change, resulting in reflection, and then EMI. To avoid 90 ° angles, the wiring should be routed to the corner at least at two 45 ° angles.
Tip 6: use vias carefully
In almost all PCB layouts, vias must be used to provide conductive connections between different layers. PCB layout engineers need to be very careful, because vias will generate inductance and capacitance. In some cases, they also produce reflections, because the characteristic impedance will change when making vias in the wiring.
It is also important to remember that the via will increase the routing length, which needs to be matched. In case of differential wiring, via holes should be avoided as far as possible. If it cannot be avoided, vias should be used in both routes to compensate for delays in the signal and return path.
Tip 7: Cable / physical shielding
Cables carrying digital circuits and analog currents will produce parasitic capacitance and inductance, causing many EMC related problems. If twisted pair cable is used, the coupling level will be kept low and the generated magnetic field will be eliminated. For high-frequency signals, shielded cables must be used, and their front and back sides are grounded to eliminate EMI interference.
Physical shielding is to wrap the whole or part of the system with a metal package to prevent EMI from entering the PCB circuit. This shielding is like a closed grounded conductive container, which can reduce the size of the antenna loop and absorb EMI.
Disclaimer: This article is transferred from other platforms and does not represent the views and positions of this site. If there is infringement or objection, please contact us to delete. thank you! |